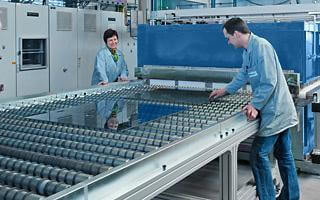
Source: berlinerglas.com
Glass is a naturally fragile material. To boost its functional properties and enhance its operational safety, it undergoes the process of tempering.
Tempering or toughening is a process where the glass is heated at high temperatures to make it stronger and more resistant to breakage. This process creates a balance in the product’s internal stresses. So, that when the glass broken. It would crumble into tiny granular chunks instead of breaking into sharp, jagged pieces.
Because of its increased strength and safety, builders and architects utilise them in a multitude of demanding applications. This includes showers, vehicle windows, refrigerator trays, glass tables, diving masks, glassware, cookware, fireplace grates, bulletproof windows, architectural glass doors and virtually anywhere else that needs safe and strong glass.
The Tempered Glass Manufacturing Process
Tempered glass goes through a process similar to that of tempered steel. Below, we take you through its sophisticated manufacturing process.
Stage 1: All toughened glass begins life as a float glass. Before it undergoes tempering, the glass examines for imperfections. Bubbles, inclusions, and cracks may cause the float glass to break during toughening. So, if any signs of such flaws found, the glass can’t temper.
Stage 2: Prior to toughening, it must first cut to the desired shape. As it won’t be possible to cut or etch the finished product in its toughened state. Once cut, the edges are smoothed and any burrs produced during etching or cutting are removed.
Stage 3: To completely remove the grains of glass that we deposited during sanding. The float glass thoroughly washed. This also ensures that dirt and any other tiny debris won’t interfere with the tempering.
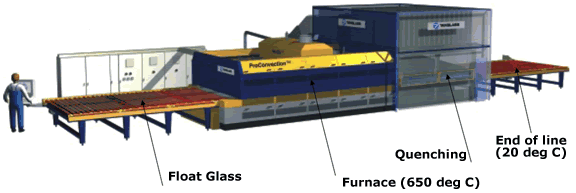
Source: breakglass.org
Stage 4: In the tempering process, the surface of the float glass heated at over 600 degrees Celsius. As it travels through a furnace. Some manufacturers heat the glass above its annealing point of approximately 720 degrees Celsius.
Stage 5: The scorching glass then rapidly cooled through quenching by a high-pressure blast of air for a period of three to 10 seconds at various angles. As it cools and begins to shrink, tensile stress temporarily build-up in the interior zone of the glass while its surface consequently develops surface stresses. These compressive stresses eventually enhance the strength of the glass, making it tougher to break.
Tempered Glass
A properly toughened glass / tempered glass should be able to withstand pressures of a minimum of 10,000 pounds per square inch (psi) and can be expected to break at about 24,000 psi.
Beyond added tensile strength and safety, toughened glass /tempered glass has a greater resistance to thermal shock and thermal stresses. Essentially, it can withstand constant exposure to temperatures as high as 243 degrees Celsius.
Despite these property enhancements, the characteristics of toughened glass / tempered glass are that of clarity chemical transmission, colour, expansion coefficient, and chemical composition (which remains unaltered).
If toughened glass / tempered glass is the right product for you contact Economy Glass with the details.